

Nelson M (1989) Smooth appearance for polygonal surfaces. Springer International Publishing AG, pp 153–174
#Wings 3d weld could not be resolved skin#
J Comput Graph Forum 31(1)Ību Rumman N, Fratarcangeli M (eds) (2017) Skin deformation methods for interactive character animation. In: Proceedings SIGGRAPH’07, San Diego, California 5–9 August 2007Ĭashman TJ (2012) Beyond Catmull–Clark? A survey of advances in subdivision surface methods. American Society for Engineering Educationīotsch M, Pauly M, Kobbelt L, Alliez P, Lévy B, Bischoff S, Rössl C (2007) Geometric modeling based on polygonal meshes. Wronecki J (2006) Concept modeling with NURBS, polygons, and subdivision surfaces. Isbister K (2006) Better game characters by design. Raab R, Gotsman C, Sheffer A (2004) Virtual woodwork: making toys from geometric models.
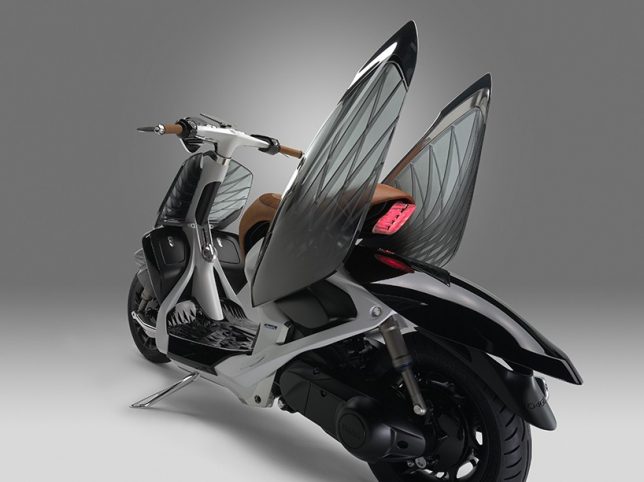
Technical Report: isda08-002 Image Spatial Data Analysis Group National Center for Supercomputing Applications, October 2008 McHenry K, Bajcs P (2008) An overview of 3d data content, file formats and viewers. In: 20th Innovative Manufacturing Engineering and Energy Conference (IManEE 2016) Kitsakis K, Kechagias J, Vaxevanidis N, Giagkopoulos D (2016) Tolerance analysis of 3d-MJM parts according to IT grade. In: Impact 6 International Printmaking Conference, Bristol, September 2009 Walters P, Huson D, Parraman C, Stanić M (2009) 3D printing in colour: technical evaluation and creative applications. The UV coordinate maps and the designed textures make it possible for the same geometry or simplified versions of the manufactured model to be modified by means of 3D animation techniques with skeletons, to be used in virtual representations and in augmented reality environments, increasingly demanded in the field of Graphic Engineering. It is, therefore, a hybrid method based on the manipulation of mesh polygons with accessible tools that is suitable for the design and manufacture of bio-inspired products, paleontological reconstructions, prostheses or bio-engineering components.
#Wings 3d weld could not be resolved free#
It has been experimentally verified that the proposed modeling methodology allows the integration of components designed by CAD, generates topologies coherent with innovative criteria that they facilitate production through additive manufacturing with related surfaces free of errors. The tangible results of the project that includes the variations of the model generated for 3D animation equipped with articulated bones are also exposed. The document shows the general flow of activities presenting in each one the particularities and resolved contingencies. Next, the stages followed for the execution of the project that give justification to the methodology developed are described. In the introduction, the boundary conditions of the project and the product to be modeled with the starting specifications are presented. It is applied to a real case of development of a sculptural element related to the corporate image of a company. This work presents a methodology of 3D modeling suitable for the design and manufacture of components with complex forms of organic inspiration.
